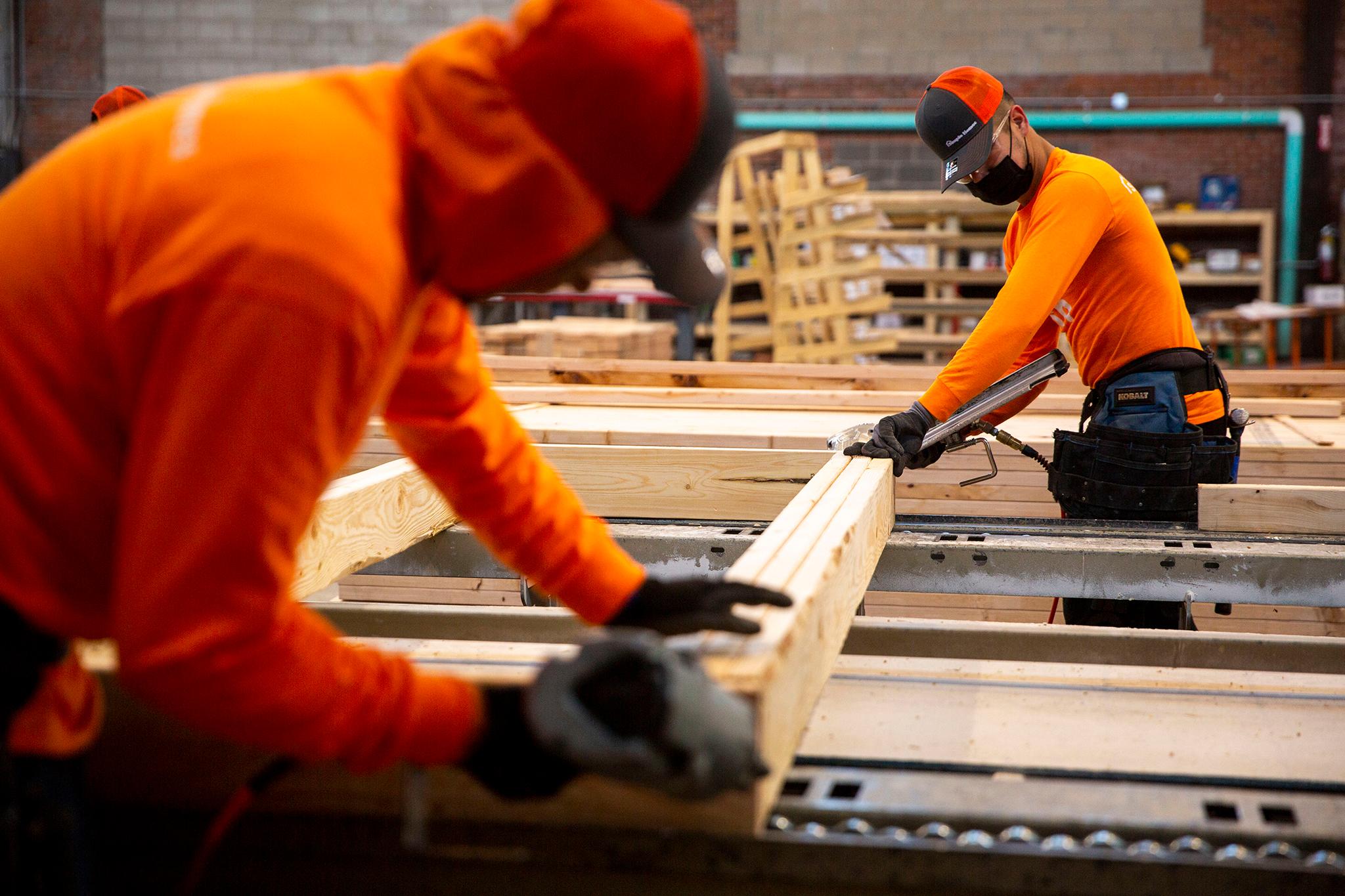
A dozen guys in orange shirts and safety glasses swarmed around a sunny warehouse floor in Denver’s Globeville neighborhood. As they worked, the cavernous brick building echoed with the punch of nail guns and the whine of power saws.
They were assembling wooden wall frames — a fundamental part of most construction projects. But they weren’t working on a construction site. Instead, this century-old warehouse has become a factory for building houses.
“Two years ago, this was just kind of a dream, and we were building our first couple houses,” said Jeff Hopfenbeck, the CEO of Simple Homes, as he watched the assembly lines.
“It’s amazing to have 50 people working for us and be building tens of thousands of square feet every single month — everything from small projects to big multifamily projects.”
Simple Homes is one of a few prefabricated housing manufacturers in Colorado — a tiny but growing segment of the construction business. The idea of building parts of structures in factories has been around for decades, but it’s drawn new focus during the recent labor crunch and housing shortage.
This year, the industry is set to get another big boost: A bipartisan proposal in the state legislature would offer $40 million in grants for “innovative” housing manufacturers. Their hope is to not just build affordable housing but to boost the overall housing supply.
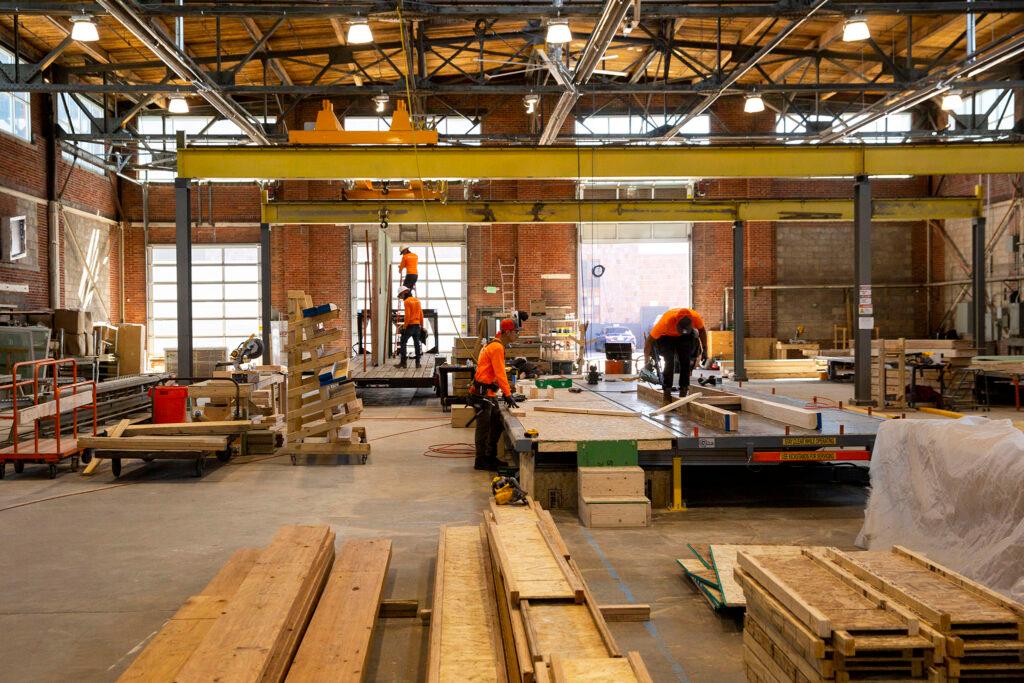
How housing factories and 'panelization' work
Simple Homes is based in a former rail yard in the Globeville neighborhood, where it focuses on a specific method known as panelization. Instead of building entire homes, its factory workers build wooden walls — or panels — that are then shipped to construction sites across the state.
“So, our flow in here basically runs north to south,” explained Hopfenbeck, a former McKinsey consultant who co-founded the company with David Schultz, a homebuilder.
On the north end of the 20,000-square-foot factory, workers use a partially automated saw to cut lumber to size. With software that monitors the factory’s supplies, the saw is able to reduce waste to about 1 percent, compared to traditional sites that might waste 15 percent of their timber, Hopfenbeck claimed.
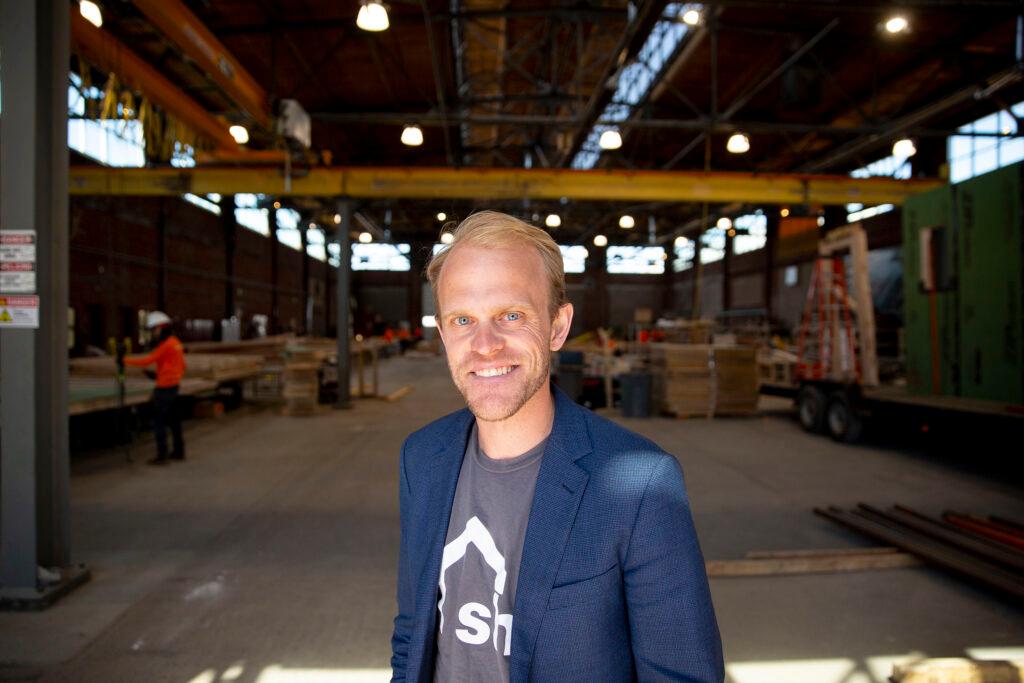
Each piece of wood is printed with assembly instructions and moved to one of three assembly lines, where a team of framers nails together a frame. The entire process is powered by detailed digital plans and customized computer software — both of which are created in an adjoining office.
“This is similar to what they do for site framing, but it’s much faster here. The guys aren’t having to cut every piece of lumber,” Hopfenbeck said.
After a series of rapid-fire nail-gun bursts, the panels are rolled down the manufacturing line. Some will have sheathing and windows installed, while others will be shipped out as simple wooden frames. Once they’re ready to go, they are picked up by an overhead bridge crane and loaded into customized trailers near the factory’s roll-up garage doors.
“We’ve been following Jeff Hopfenbeck for quite some time, and he’s got a pretty amazing product,” said Kimball Crangle, an affordable housing developer who isn’t affiliated with the company.
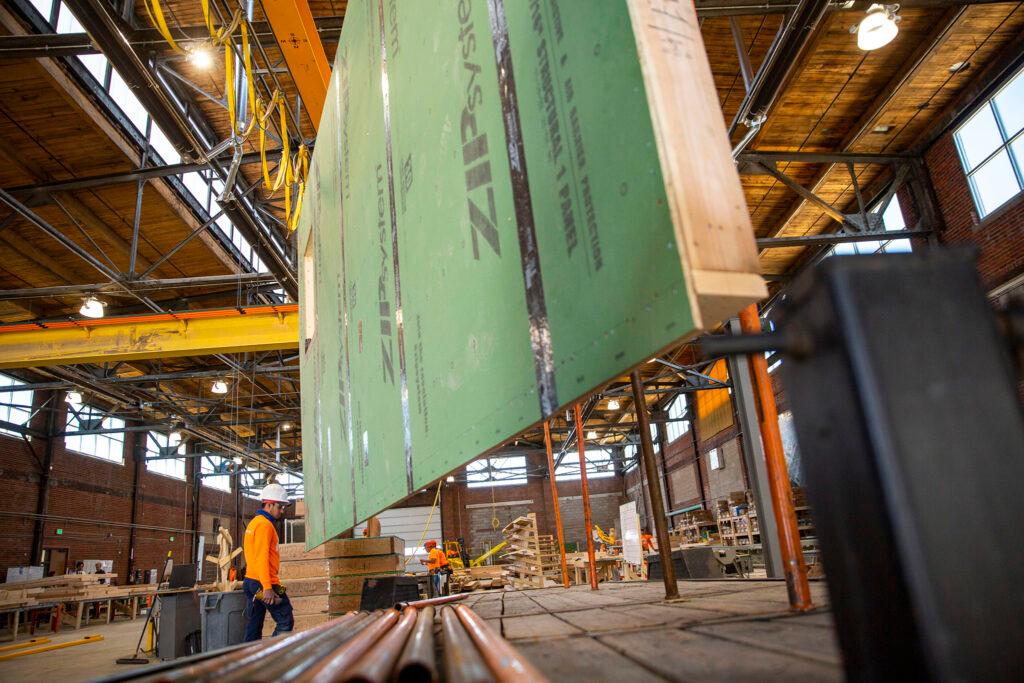
She described Simple Homes as an incremental improvement on homebuilding. It’s not always cheaper than traditional construction, but it requires much less time and labor on the site. That’s appealing for homebuilders who are dealing with labor shortages and tight construction schedules.
“When we’re building in far reaches of the state, you can’t often find the same crews that you can if you’re in metro Denver, and so the industry has had to become more efficient,” Crangle said.
Major builders have already started to use prebuilt panels in some projects. But what makes Simple Homes notable is the efficiency and design of its factory setup, Crangle said.
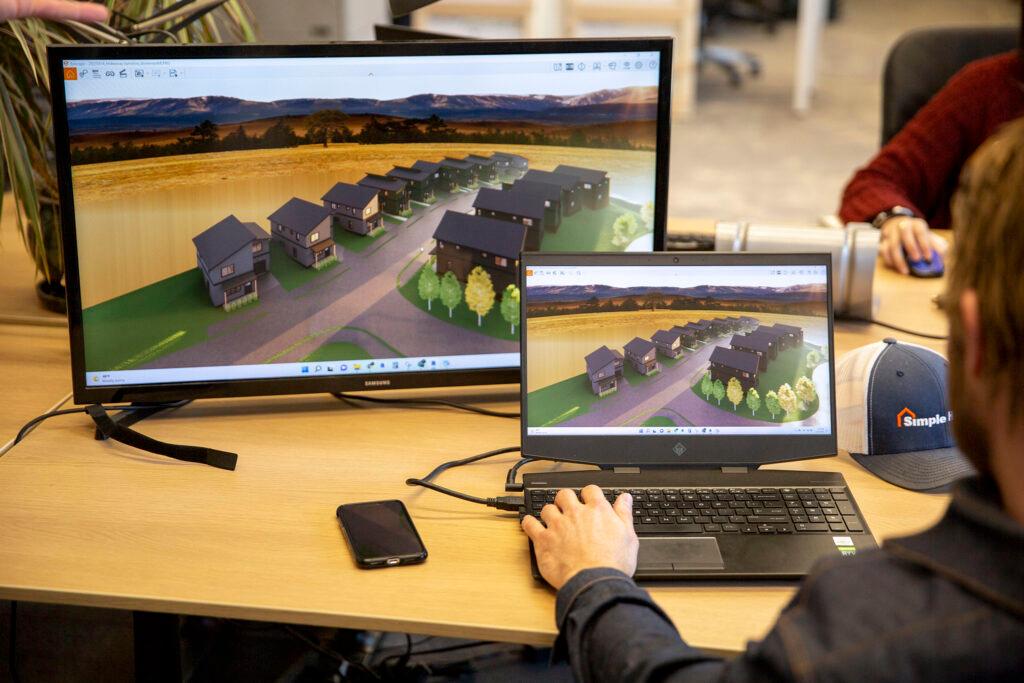
Colorado lawmakers are fans of the approach, and they're prepared to fund it
State lawmakers also see potential in this approach. They’re currently crafting a $400 million housing package using one-time federal relief money. Most of that funding will go toward grants and loans for specific housing developments, but $40 million would be offered to companies like Simple Homes.
“I hope that it's like a jumpstart to the industry and that it really gives us a different opportunity, and that we view housing a little differently,” said state Rep. Kyle Mullica, a Democratic sponsor of the bill.
Prefabricated housing manufacturers could get grants to help them with capital costs, such as installing a new factory line. They also could get incentives if they build units that meet certain criteria, such as affordability, location and energy efficiency.
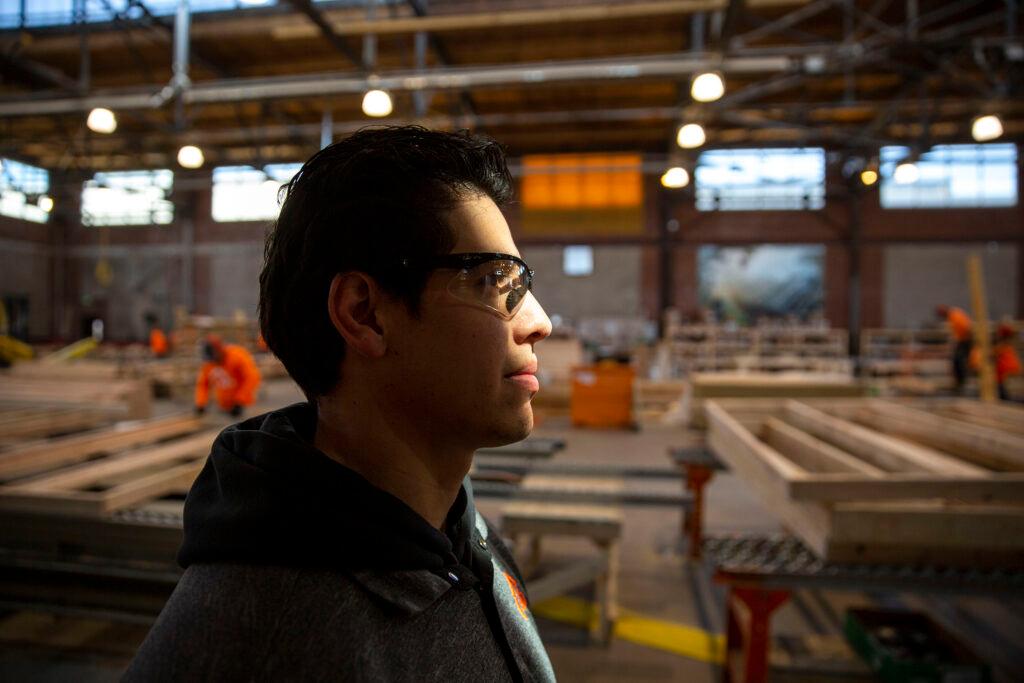
The money would be available for companies that specialize in everything from 3D printing to mobile homes. It could also go toward “modular” builders — who, instead of making flat surfaces like walls, build three-dimensional rooms. They can install fixtures and finishings, or even complete an entire home on the factory floor.
Pete Gombert is the executive chairman of indieDwell, which opened a modular housing factory in Pueblo in 2020. He said that state money could help seed the housing manufacturing industry, including in communities that have suffered a decline in manufacturing.
“We’re hopeful that it advances the whole industry so that you’ve got more players, more innovation and more awareness of what’s possible, and how to do it,” Gombert said.
The industry remains “extremely” small, Gombert said. Other notable Colorado companies include the modular builder Fading West in Buena Vista and the developer Milender White’s prefabricated wood shop in Hudson.
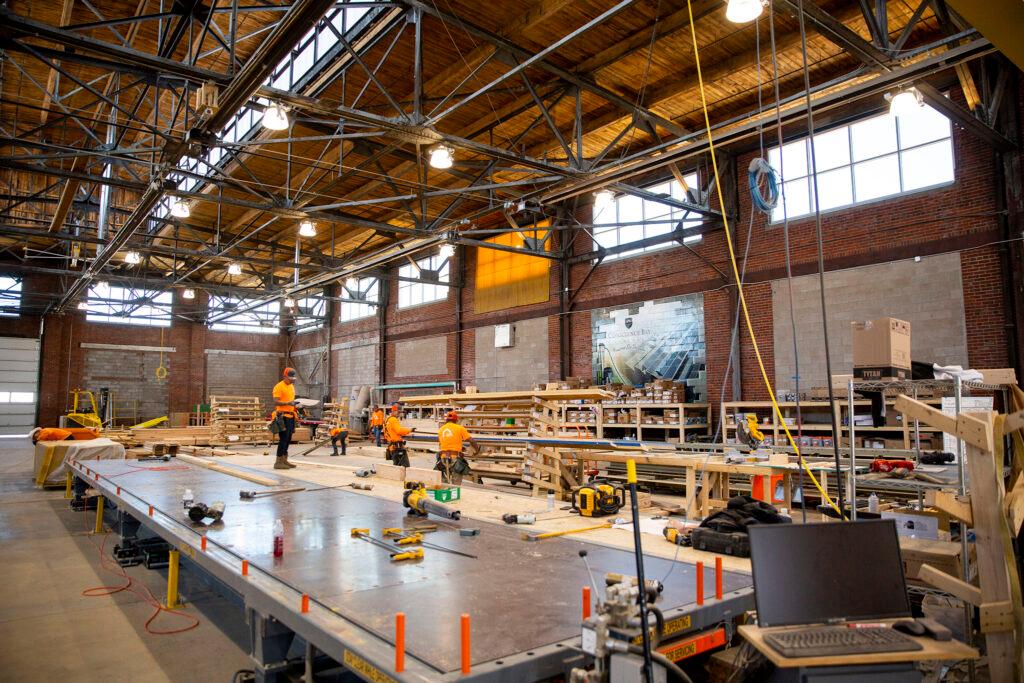
It’s unclear just how far the state’s $40 million program could go to boosting these companies. For comparison, Simple Homes has taken about $5 million in investor dollars, plus a $1 million federal grant for research into automation and robotics. The company recently turned profitable, Hopfenbeck said.
Stepping out of the factory, Hopfenbeck pointed out dozens of completed wooden frames waiting for shipment across the state.
“We have multiple projects here,” he said. “This is for an eight-unit townhome project, that’s for a single-family home in Aurora, and that stack out there is for a 50,000 square-foot apartment building.”
Eventually, he hopes to produce materials for thousands of homes per year and turn this North Denver startup into a national force in the construction industry. In this housing market, they’ve got plenty of room to build.
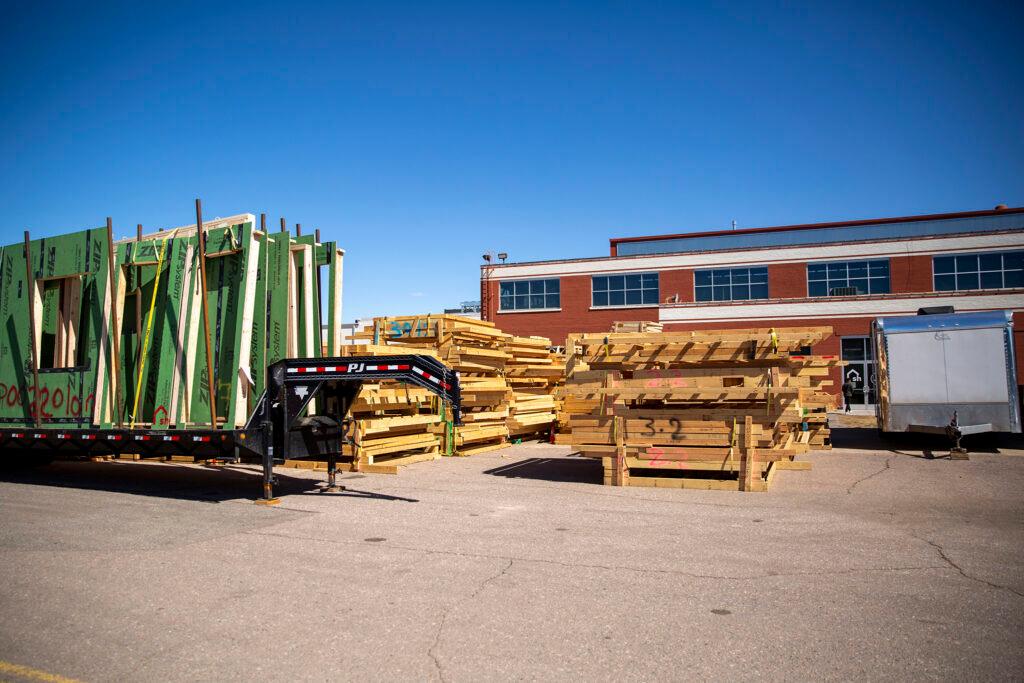